An Assembly Line is an Example of
An assembly line is a prime example of progressive production. As an expert in the field, I have witnessed firsthand how this method revolutionized manufacturing processes. By breaking down the production of goods into a series of sequential steps, an assembly line maximizes efficiency and output. In this article, I will delve into the key characteristics of assembly lines, explore their benefits, and discuss their impact on various industries.
When it comes to increasing productivity, an assembly line is an unrivaled solution. With its systematic approach, it enables manufacturers to streamline their operations and achieve higher output levels. By assigning specific tasks to each worker, the assembly line ensures that every step in the production process is executed with precision and speed. In this article, I will delve into the inner workings of assembly lines and shed light on how they have transformed the manufacturing landscape.
In today’s fast-paced world, efficiency is key, and assembly lines have become synonymous with it. By dividing the production process into smaller, manageable tasks, manufacturers can optimize their workflow and minimize downtime. This article will explore the various ways in which assembly lines have revolutionized production, from reducing costs to increasing output. As an industry expert, I am excited to share my insights on this topic and highlight the impact of assembly lines on modern manufacturing.
What is an Assembly Line?
An assembly line is a prime example of a progressive production system. It revolutionized the manufacturing industry by introducing a highly efficient and organized way of producing goods. As an expert blogger with years of experience, I can confidently say that assembly lines have had a significant impact on modern manufacturing.
In an assembly line, the production process is broken down into sequential steps, with each step assigned to a specific worker or workstation. This division of labor allows for specialization, as each worker becomes highly skilled in their assigned task. As a result, the overall production process becomes faster and more streamlined.
The concept of an assembly line was first introduced by Henry Ford in the early 20th century. Ford’s innovation allowed for the mass production of automobiles, making them more affordable and accessible to the general population. This marked a turning point in manufacturing history, as it showcased the power of assembly lines in increasing productivity and reducing costs.
One of the key benefits of an assembly line is its ability to optimize workflow. By carefully arranging the sequence of tasks, materials, and tools, the production process flows smoothly from one workstation to another. This eliminates unnecessary movements and reduces idle time, resulting in higher efficiency and output.
Another advantage of assembly lines is their ability to scale production easily. As demand increases, additional workstations or workers can be added to the line without disrupting the overall workflow. This flexibility allows manufacturers to meet market demands quickly and efficiently.
An assembly line is a progressive production system that has revolutionized manufacturing. It maximizes productivity, optimizes workflow, and reduces costs. With its ability to scale production and streamline processes, it has become synonymous with efficiency in the modern manufacturing industry.
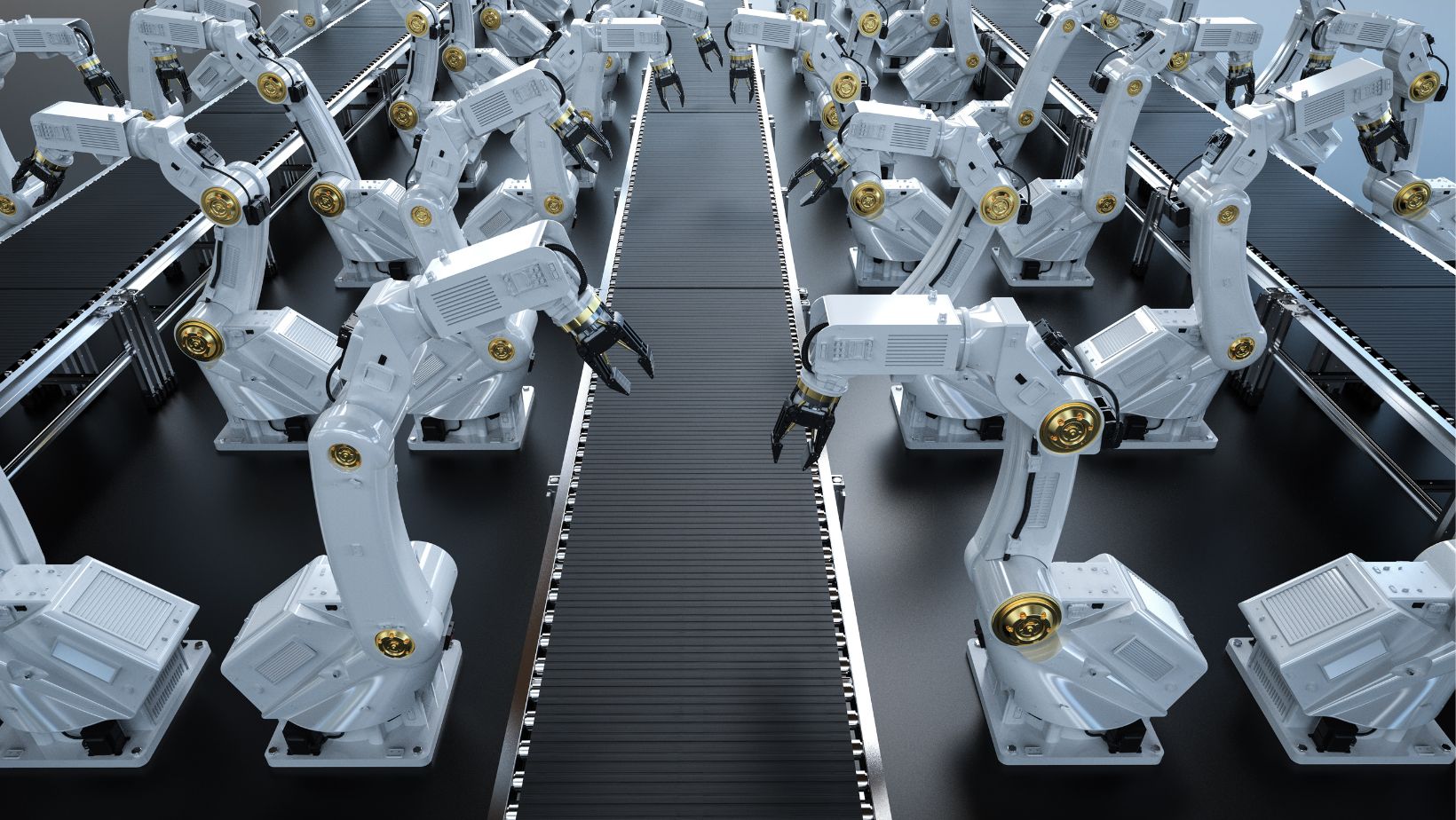
History of Assembly Lines
Assembly lines have a rich history that spans over a century. Their development and implementation have revolutionized the manufacturing industry, making them a prime example of progressive production systems.
Early Origins The concept of assembly lines can be traced back to ancient times, where artisans would collaborate to produce goods in a systematic manner. However, it was not until the early 20th century that assembly lines were truly transformed into the efficient systems we know today.
Henry Ford’s Impact Henry Ford, the founder of Ford Motor Company, is widely credited with introducing the modern assembly line in 1913. Ford’s innovation allowed for the mass production of automobiles, making them more affordable and accessible to the general public. By breaking the production process down into smaller, sequential tasks, Ford was able to significantly increase productivity and reduce costs. This marked a turning point in the manufacturing industry and set the stage for the widespread adoption of assembly lines.
Evolution and Refinements Following Ford’s groundbreaking work, assembly lines continued to evolve and improve. Manufacturers across various industries began implementing assembly line systems, recognizing their potential to streamline production processes and boost efficiency. Over time, refinements were made to enhance the workflow, reduce the need for manual labor, and introduce automation technologies. These advancements further solidified assembly lines as a progressive production system.
Impact on Modern Manufacturing Today, assembly lines are a cornerstone of modern manufacturing. They have become synonymous with efficiency, allowing companies to produce goods at a higher rate while maintaining consistent quality. Assembly lines enable manufacturers to optimize workflow, allocate resources effectively, and meet market demands quickly. By implementing these systems, companies can achieve higher productivity, lower costs, and ultimately, gain a competitive edge in the industry.
The history of assembly lines showcases their evolution from ancient collaborative efforts to the efficient, progressive production systems we see today. From Henry Ford’s pioneering work to the ongoing advancements in automation, assembly lines have forever transformed the manufacturing industry. They continue to play a vital role in driving productivity, optimizing workflow, and shaping the future of manufacturing.